Dartmouth is always under construction. Right now, the Hopkins Center for the Arts, Rauner Special Collections Library and the East Wheelock dorms are all being renovated. In the past four years, the College has built Anonymous Hall, Arthur L. Irving Institute for Energy and Society and the Engineering and Computer Science Center. It has also renovated several existing buildings including Dartmouth Hall, Thornton Hall and the Nelson A. Rockefeller Center for Public Policy and the Social Sciences. Innovation in construction technology — especially concrete — is an important step towards decarbonization for Dartmouth and for the rest of the developed and developing world. Federal investment in research and development will pay dividends for climate and infrastructure.
The manufacture of concrete emits carbon dioxide in two ways, both involving the synthesis of cement, the active ingredient in concrete. First, the chemical process that turns limestone into cement releases carbon dioxide — these are called “process emissions.” Second, this process occurs in an ultra-hot kiln that consumes significant energy, which is often provided by carbon-emitting sources. Together, these sources account for 77% percent of concrete emissions. Energy used in mining, processing and transport accounts for the remaining 23%.
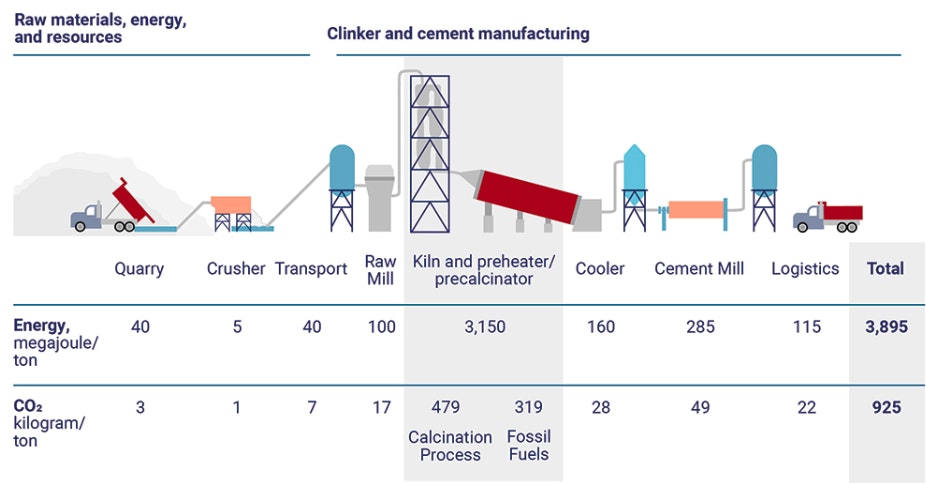
Total emissions from the concrete industry contributed to 8% of all global emissions in 2023. This number will likely grow in the coming years, as global cement demand is expected to increase 48% to 6.2 billion tons per year by 2050.
Unfortunately, there is no publicly available information on the amount of concrete that Dartmouth has used in construction. However, some back-of-the-envelope calculations can provide a rough sense of the emissions caused by concrete construction at Dartmouth.
Every pound of cement produces about 0.9 pounds of carbon dioxide in the course of manufacturing. Cement is then mixed with water and other ingredients to create concrete. In construction-standard recipes, one cubic yard of concrete (about 3900 pounds) is responsible for about 400 pounds of emitted carbon dioxide.
Suppose that the buildings at Dartmouth use concrete in the same proportions as those of a 1500 square-foot home: about 1.2 cubic feet of cement for every square foot of floor area. The square footage of campus buildings totaled 6.5 million in 2022, which implies that Dartmouth’s lifetime carbon dioxide emissions from concrete sit somewhere near 52,000 metric tons (MT). For context, Dartmouth’s total emissions from energy consumption per year are only slightly higher, at 58,499 MT in 2022.
Of course, this is a rough calculation based on imperfect assumptions. It is plausible that large multistory buildings like the ECSC use less concrete per square foot than a 1500-square-foot home. But even at a rate of only one cubic foot of cement per square foot of floor area, the construction of the ECSC alone emits roughly 1075 MT of carbon dioxide, or just under 2% of Dartmouth’s total 2022 emissions. It is also likely that some concrete structures have been replaced throughout Dartmouth’s lifetime, meaning that my estimates based on present square footage are too low.
Roughshod calculations notwithstanding, it is clear that emissions from concrete have meaningfully contributed to Dartmouth’s emissions, both historically and in the recent past. In the published information about the construction of the ECSC, Irving or any other recent construction project, there is no evidence that Dartmouth prioritized the use of low-emissions concrete or otherwise accounted for the emissions impact of the material.
More surprisingly, the LEED certification earned by many of Dartmouth’s recently constructed buildings makes no mention of emissions from concrete. In the 312-page document detailing the LEED requirements for a building’s design and construction, concrete is only mentioned as a material to be exempted from restrictions on materials that produce harmful vapors. There appears to be no penalty for using carbon-emitting concrete, and no reward for replacing the material with cleaner alternatives.
Though Dartmouth administration appears unconcerned by emissions from concrete, they rightly emphasize energy consumption and heating/cooling efficiency as by far the largest drivers of emissions at Dartmouth. Concrete emissions pale in comparison to the amount of carbon dioxide emitted by the generators that create steam to heat campus buildings every winter. All new buildings at Dartmouth, including ECSC and Irving, are outfitted with heat pumps that will aid Dartmouth’s transition away from this dirty, fuel-powered steam heating.
In this context, my prescription for the administration is moderate. First, they should make public the amount of concrete used in past and future construction projects, and account for the related carbon dioxide emissions on the tracker on their website. My back-of-the-envelope math can definitely be improved.
Second, Dartmouth should prioritize low-carbon concrete technologies in future construction projects. There are several companies developing cleaner manufacturing processes for cement or alternative materials. Heidelberg Materials is developing technology to capture and store carbon emitted from the production of cement. Brimstone and Sublime Systems are both developing alternative chemical pathways for cement that eliminate the process emissions produced by the conventional method. Most excitingly, CarbonBuilt is developing a method of curing concrete that sequesters carbon dioxide from a point source or from ambient air. These new technologies become more cost-effective each year, and they should play a central role in Dartmouth’s future construction.
There are also significant policy opportunities at the federal level. The Department of Energy’s carbon capture research and development program should expand its focus on industrial applications, including concrete manufacturing. Because the cement production market is highly competitive, however, manufacturers are unlikely to use costly carbon capture and storage technology (CCS), even with tax incentives. On the demand side, the federal government can incentivize the purchase of low-carbon concrete by piloting advance market commitments (AMCs) — contracts that guarantee profitability for undeveloped technology — to ensure the future profitability of CCS and other low-carbon concrete technologies. These incentives will hasten innovation and ensure that Dartmouth’s future construction will be cost-effective and low-carbon.
Opinion articles represent the views of their author(s), which are not necessarily those of The Dartmouth.